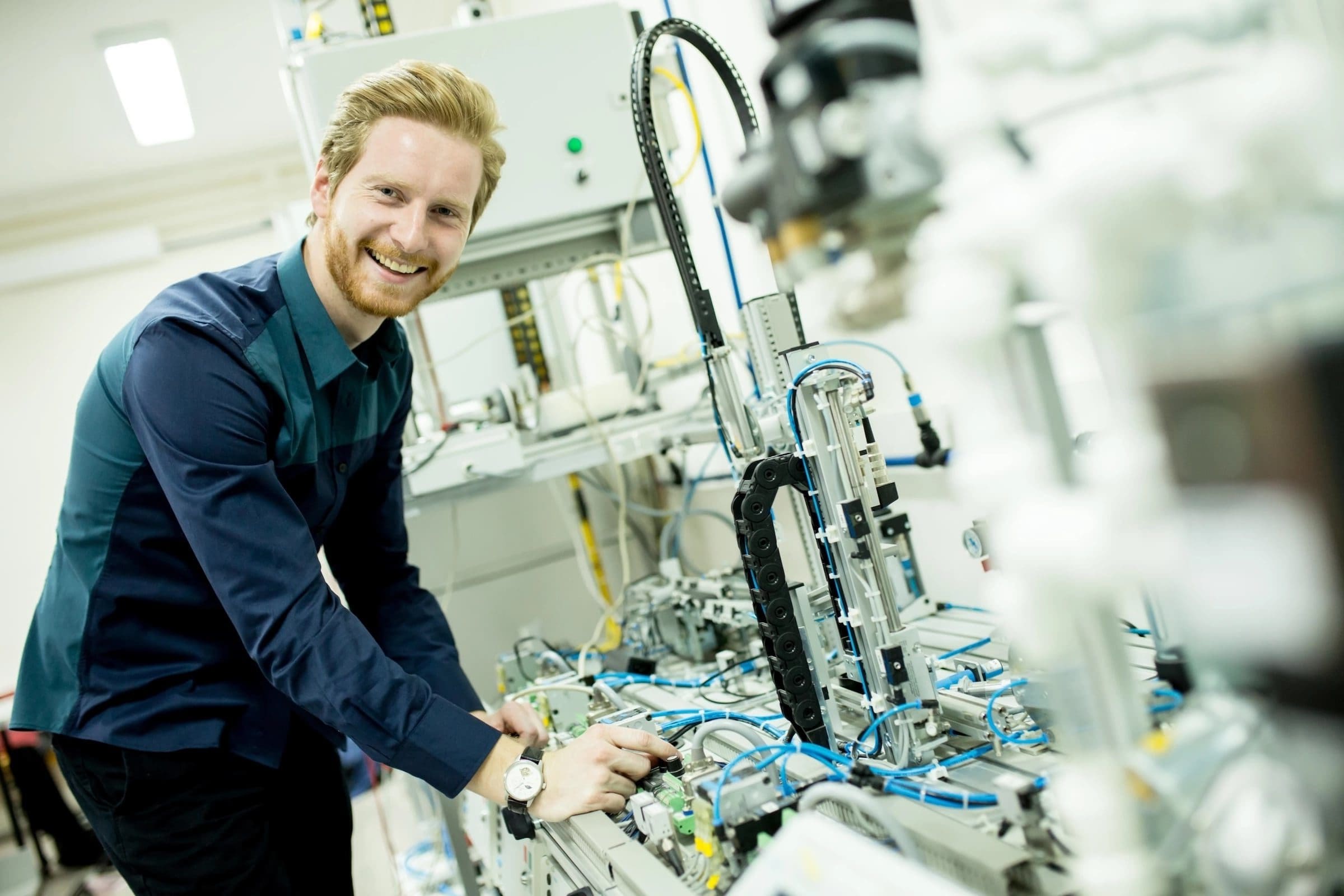
Electro-Mechanical Technology
Get started today
About Electro-Mechanical Technology
The Electro-Mechanical Technology Associate Degree program prepares students to work at the intersection of mechanical systems, electronics, and industrial automation. Students gain hands-on experience with PLCs, sensors, motors, hydraulics, pneumatics, and robotic systems used in modern manufacturing environments. The curriculum emphasizes troubleshooting, system integration, and maintenance of electromechanical equipment. Coursework includes AC/DC circuits, industrial wiring, mechanical drives, fluid power, process control, robotics, and programmable logic controllers. Graduates are equipped to interpret technical drawings, program automated systems, and ensure efficient operation of machinery. This program is ideal for careers in industrial maintenance, automation, and advanced manufacturing support.
What you’ll learn
- Disassemble machinery or equipment to remove parts and make repairs.
- Repair or replace broken or malfunctioning components of machinery or equipment.
- Repair or maintain the operating condition of industrial production or processing machinery or equipment.
- Examine parts for defects, such as breakage or excessive wear.
- Reassemble equipment after completion of inspections, testing, or repairs.
- Observe and test the operation of machinery or equipment to verify the adequacy of repairs.
- Clean, lubricate, or adjust parts, equipment, or machinery.
- Analyze test results, machine error messages, or information obtained from operators to diagnose equipment problems.
- Record repairs and maintenance performed.
- Read, write, and edit PLC programs.
- Install, troubleshoot, and repair PLC I/O wiring.
- Install, troubleshoot, and repair power distribution systems.
- Install, troubleshoot, and repair electrical wiring and circuitry.
- Install, troubleshoot, and replace AC, DC, and 3-phase motors.
- Install, troubleshoot, and replace proximity sensors, photo-eyes, magnetic switches and other sensors.
- Install, troubleshoot, and replace motor controls such as variable frequency drives and across the line starters.
- Install, troubleshoot, and repair temperature control systems using thermocouples and RTDs.
Sample Job Titles
Perform work involving the skills of two or more maintenance or craft occupations to keep machines, mechanical equipment, or the structure of a building in repair. Duties may involve pipe fitting; HVAC maintenance; insulating; welding; machining; carpentry; repairing electrical or mechanical equipment; installing, aligning, and balancing new equipment; and repairing buildings, floors, or stairs.
Building Maintenance Mechanic, Building Mechanic, Equipment Engineering Technician, Maintenance Engineer, Maintenance Man, Maintenance Mechanic, Maintenance Technician, Maintenance Worker
Quick facts
Location
Kreider Building, Main Campus
Type of program
Associate Degree
Length of program
2 years, 73 credits
Job/Salary Outlook
View industry data
Cost of program
$4,500/semester tuition
$3,000 – $3,500/semester housing
$1,850 – $2,335/semester meal plan
Tool List (PDF)
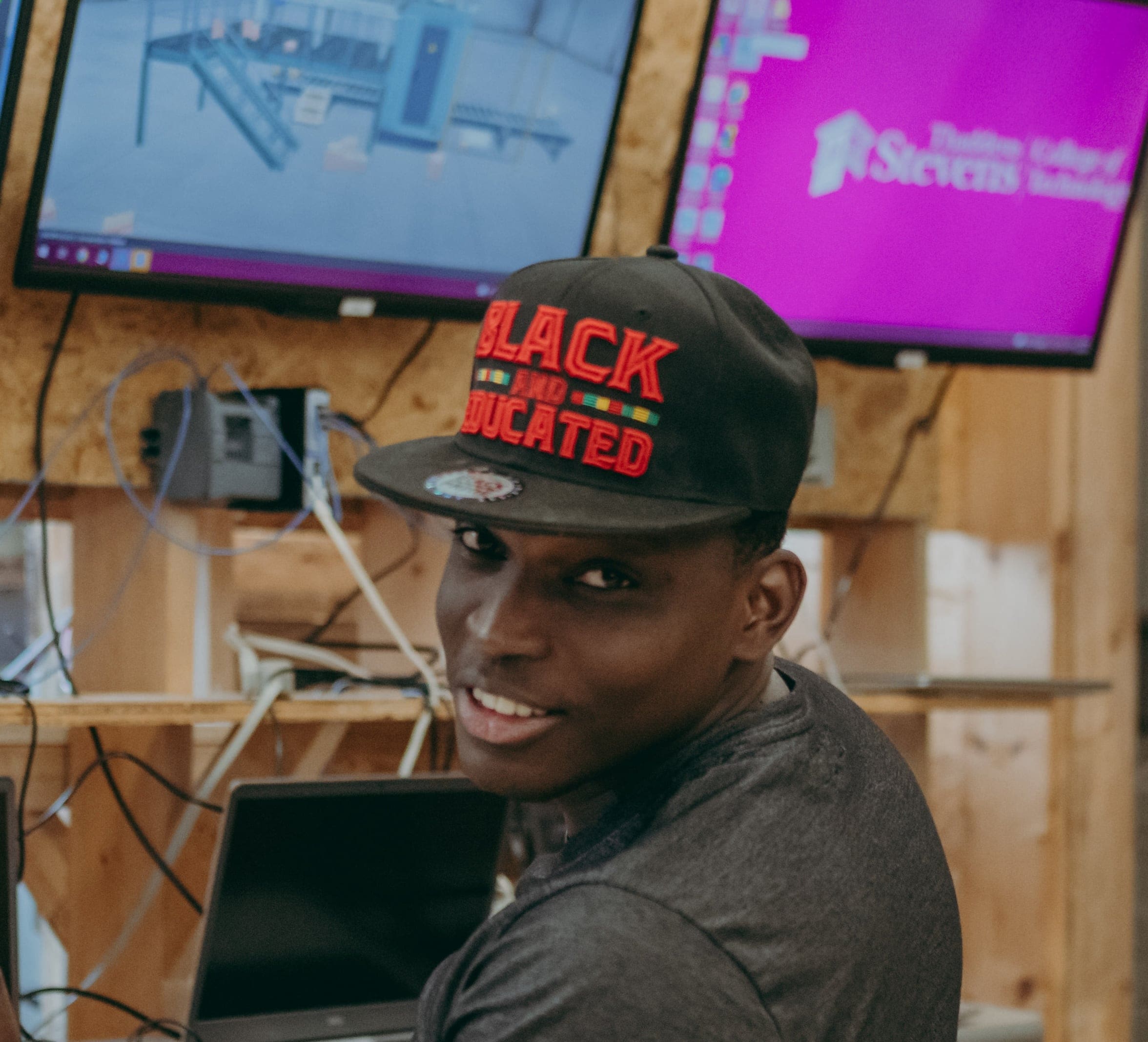
The outcomes speak for themselves
Also known as mechatronics, this program combines electrical and mechanical skills to train graduates in maintaining machines and mechanical equipment.
94.7%
employment
$72.5K
med. salary
People of TSCT
Success stories
Program details
Courses
MODEL SCHEDULE FOR ELECTRO-MECHANICAL TECHNOLOGY
Semester 1
- ELME 104 Mechanical Systems I (4 credits)
- ELME 105 Manufacturing Fundamentals (4 credits)
- ELME 107 Electrical Systems I (4 credits)
- MATH 137 Intermediate Algebra 3 or MATH 207 Pre-Calculus (4 credits)
- ENG 106 Composition I (3 credits)
Semester 2
- ELME 109 Programmable Logic Controllers I (4 credits)
- ELME 116 Mechanical Systems II (4 credits)
- ELME 117 Electrical Systems II (4 credits)
- MATH 141 Trigonometry or higher (3 credits)
- ENG 216 Technical Writing (3 credits)
Semester 3
- ELME 204 Mechanical Systems III (4 credits)
- ELME 208 Programmable Logic Controllers II (4 credits)
- ELME 215 Robotics and Motion Control (4 credits)
- HUMANITIES ELECTIVE (3 credits)
- PHYS 213 General Physics | (4 credits)
Semester 4
- ELME 214 Mechatronics Seminar & Advanced Project (4 credits)
- ELME 218 Process Control and
- Industrial Instrumentation (4 credits)
- ELME 225 Computer Integrated Manufacturing
- Systems & PLC III (4 credits)
- GENERAL STUDIES ELECTIVES (3 credits)
Additional General Education Requirements
- ELECTIVE General Education Elective 3
- ELECTIVE General Studies Elective (only w/Pre-Calculus) 3
Total Credits 73
Faculty
Occupational Advisory Committee
The Occupational Advisory Committee (OAC) serves as a vital link between the Program of study and industry, ensuring that the program remains aligned with current workforce needs, technological advancements, and best practices in the field. Composed of employers, educators, and other community members, the committee provides guidance, feedback, and recommendations to enhance the curriculum, instructional methods, and student learning experiences.
Purpose and Responsibilities:
- Curriculum & Industry Alignment
- Workforce Readiness
- Student & Faculty Support
- Internship & Employment Connections
- Accreditation & Program Evaluation
- Facilities & Equipment Recommendations
By fostering a strong relationship between academia and industry, the OAC helps ensure that Thaddeus Stevens College programs maintain the highest standards in CTE (career and technical education).
- Michael Baron, Retired
- Randy Blair, Heat and Control
- Jim Brandt, Multi-Dimensional Integration
- Juana Caudillo-Zavala, SFS Group
- Don Dagen, Roechling Medical Lancaster
- Jim Dawalt, Hillside Custom
- Felix DeJesus, Armstrong World Industries
- Amy Doyle, Cardinal Systems, Inc.
- Shane Findley, J.L. Clark
- Justin Fisher, Americold
- Charles Gales, Weldon Solutions
- Michael Gerfin, Retired
- Kim Gibson, National Novelty Brush Co.
- Brian Hammer, ACME Distribution Center
- Bill Hapke, National Novelty Brush Co.
- Jim Lehman, Festo Corp.
- Kyle Lumbert, PepsiCo-Frito Lay
- Melissa Martin, Viocity Group
- Rick Naranjo, Paradise Energy Solutions
- Kevin Neuman, Astro Machine Works
- Chris Riportella, Conestoga Wood Specialties
- Daniel Rogers, United Equipment Limited
- Laura Schoonover, Actalent
- Steven Shriver, Shingle & Gibb Automation
- Terry Speicher, Penn State Berks
- Kurt Suchar, KH
- Gene Walter, J. L. Clark
- Christian Wise, Cargill
Essential Skills Learned
Tasks
- Inspect, operate, or test machinery or equipment to diagnose machine malfunctions.
- Dismantle machines, equipment, or devices to access and remove defective parts, using hoists, cranes, hand tools, or power tools.
- Perform routine maintenance, such as inspecting drives, motors, or belts, checking fluid levels, replacing filters, or doing other preventive maintenance actions.
- Diagnose mechanical problems and determine how to correct them, checking blueprints, repair manuals, or parts catalogs, as necessary.
- Repair machines, equipment, or structures, using tools such as hammers, hoists, saws, drills, wrenches, or equipment such as precision measuring instruments or electrical or electronic testing devices.
- Maintain or repair specialized equipment or machinery located in cafeterias, laundries, hospitals, stores, offices, or factories.
- Assemble, install, or repair wiring, electrical or electronic components, pipe systems, plumbing, machinery, or equipment.
- Clean or lubricate shafts, bearings, gears, or other parts of machinery.
- Adjust functional parts of devices or control instruments, using hand tools, levels, plumb bobs, or straightedges.
- Order parts, supplies, or equipment from catalogs or suppliers.
- Plan and layout repair work, using diagrams, drawings, blueprints, maintenance manuals, or schematic diagrams.
Tools used in this occupation
- Drain or pipe cleaning equipment — Drain augers; Drain cleaning cables; Hand spinners; Power drain cleaners
- Pipe or tube cutter — Pipe cutters; Power pipe cutters; Ratcheting polyvinyl chloride PVC cutters; Tubing cutters
- Power drills — Cordless power drills; Direct tap machines; Hammer drills; Right-angle drills
- Power saws — Circular saws; Radial arm saws; Reciprocating saws; Tile saws
- Pullers — Bearing pullers; Chain pullers; Comealongs; Tub drain removers
Technology used in this occupation
- Computer-aided design CAD software — Autodesk AutoCAD; Computer aided design and drafting software CADD; Dassault Systemes CATIA; PTC Creo Parametric
- Electronic mail software — IBM Notes; Microsoft Exchange; Microsoft Outlook
- Operating system software — Apple macOS; Handheld computer device software; Linux; Microsoft Windows
- Video creation and editing software — Loom; YouTube
- Word processing software — Google Docs; Microsoft Word
Knowledge
- Mechanical — Knowledge of machines and tools, including their designs, uses, repair, and maintenance.
- Building and Construction — Knowledge of materials, methods, and the tools involved in the construction or repair of houses, buildings, or other structures such as highways and roads.
- Customer and Personal Service — Knowledge of principles and processes for providing customer and personal services. This includes customer needs assessment, meeting quality standards for services, and evaluation of customer satisfaction.
- Public Safety and Security — Knowledge of relevant equipment, policies, procedures, and strategies to promote effective local, state, or national security operations for the protection of people, data, property, and institutions.
- English Language — Knowledge of the structure and content of the English language including the meaning and spelling of words, rules of composition, and grammar.
Skills
- Equipment Maintenance — Performing routine maintenance on equipment and determining when and what kind of maintenance is needed.
- Repairing — Repairing machines or systems using the needed tools.
- Troubleshooting — Determining causes of operating errors and deciding what to do about it.
- Critical Thinking — Using logic and reasoning to identify the strengths and weaknesses of alternative solutions, conclusions, or approaches to problems.
- Equipment Selection — Determining the kind of tools and equipment needed to do a job.
- Monitoring — Monitoring/Assessing performance of yourself, other individuals, or organizations to make improvements or take corrective action.
- Operation and Control — Controlling operations of equipment or systems.
- Operation Monitoring — Watching gauges, dials, or other indicators to make sure a machine is working properly.
- Active Learning — Understanding the implications of new information for both current and future problem-solving and decision-making.
Abilities
- Arm-Hand Steadiness — The ability to keep your hand and arm steady while moving your arm or while holding your arm and hand in one position.
- Manual Dexterity — The ability to quickly move your hand, your hand together with your arm, or your two hands to grasp, manipulate, or assemble objects.
- Near Vision — The ability to see details at close range (within a few feet of the observer).
- Information Ordering — The ability to arrange things or actions in a certain order or pattern according to a specific rule or set of rules (e.g., patterns of numbers, letters, words, pictures, mathematical operations).
- Problem Sensitivity — The ability to tell when something is wrong or is likely to go wrong. It does not involve solving the problem, only recognizing there is a problem.
- Finger Dexterity — The ability to make precisely coordinated movements of the fingers of one or both hands to grasp, manipulate, or assemble very small objects.
- Multilimb Coordination — The ability to coordinate two or more limbs (for example, two arms, two legs, or one leg and one arm) while sitting, standing, or lying down. It does not involve performing the activities while the whole body is in motion.
- Visualization — The ability to imagine how something will look after it is moved around or when its parts are moved or rearranged.
- Static Strength — The ability to exert maximum muscle force to lift, push, pull, or carry objects.
- Control Precision — The ability to quickly and repeatedly adjust the controls of a machine or a vehicle to exact positions.
- Deductive Reasoning — The ability to apply general rules to specific problems to produce answers that make sense.
Work Activities
- Inspecting Equipment, Structures, or Material — Inspecting equipment, structures, or materials to identify the cause of errors or other problems or defects.
- Handling and Moving Objects — Using hands and arms in handling, installing, positioning, and moving materials, and manipulating things.
- Performing General Physical Activities — Performing physical activities that require considerable use of your arms and legs and moving your whole body, such as climbing, lifting, balancing, walking, stooping, and handling of materials.
- Getting Information — Observing, receiving, and otherwise obtaining information from all relevant sources.
- Repairing and Maintaining Mechanical Equipment — Servicing, repairing, adjusting, and testing machines, devices, moving parts, and equipment that operate primarily on the basis of mechanical (not electronic) principles.
- Establishing and Maintaining Interpersonal Relationships — Developing constructive and cooperative working relationships with others, and maintaining them over time.
- Monitor Processes, Materials, or Surroundings — Monitoring and reviewing information from materials, events, or the environment, to detect or assess problems.
- Identifying Objects, Actions, and Events — Identifying information by categorizing, estimating, recognizing differences or similarities, and detecting changes in circumstances or events.
- Making Decisions and Solving Problems — Analyzing information and evaluating results to choose the best solution and solve problems.
- Communicating with Supervisors, Peers, or Subordinates — Providing information to supervisors, co-workers, and subordinates by telephone, in written form, e-mail, or in person.
Work Context
- Face-to-Face Discussions — 92% responded “Every day.”
- Spend Time Using Your Hands to Handle, Control, or Feel Objects, Tools, or Controls — 72% responded “Continually or almost continually.”
- Wear Common Protective or Safety Equipment such as Safety Shoes, Glasses, Gloves, Hearing Protection, Hard Hats, or Life Jackets — 74% responded “Every day.”
- Exposed to Contaminants — 65% responded “Every day.”
- Spend Time Standing — 52% responded “Continually or almost continually.”
- Contact With Others — 58% responded “Constant contact with others.”
- Importance of Being Exact or Accurate — 44% responded “Very important.”
- Exposed to Hazardous Equipment — 47% responded “Once a week or more but not every day.”
- Frequency of Decision Making — 63% responded “Every day.”
- Structured versus Unstructured Work — 53% responded “Some freedom.”
- Work With Work Group or Team — 38% responded “Extremely important.”
- Freedom to Make Decisions — 46% responded “A lot of freedom.”
Interests
- Realistic — Realistic occupations frequently involve work activities that include practical, hands-on problems, and solutions. They often deal with plants, animals, and real-world materials like wood, tools, and machinery. Many of the occupations require working outside and do not involve a lot of paperwork or working closely with others.
- Investigative — Investigative occupations frequently involve working with ideas and require an extensive amount of thinking. These occupations can involve searching for facts and figuring out problems mentally.
- Conventional — Conventional occupations frequently involve following set procedures and routines. These occupations can include working with data and details more than with ideas. Usually, there is a clear line of authority to follow.
Work Styles
- Integrity — Job requires being honest and ethical.
- Attention to Detail — Job requires being careful about detail and thorough in completing work tasks.
- Cooperation — Job requires being pleasant with others on the job and displaying a good-natured, cooperative attitude.
- Dependability — Job requires being reliable, responsible, and dependable, and fulfilling obligations.
- Independence — Job requires developing one’s own ways of doing things, guiding oneself with little or no supervision, and depending on oneself to get things done.
- Self-Control — Job requires maintaining composure, keeping emotions in check, controlling anger, and avoiding aggressive behavior, even in very difficult situations.
- Concern for Others — Job requires being sensitive to others’ needs and feelings and being understanding and helpful on the job.
- Adaptability/Flexibility — Job requires being open to change (positive or negative) and to considerable variety in the workplace.
- Analytical Thinking — Job requires analyzing information and using logic to address work-related issues and problems.
- Initiative — Job requires a willingness to take on responsibilities and challenges.
- Persistence — Job requires persistence in the face of obstacles.
Work Values
- Support — Occupations that satisfy this work value offer supportive management that stands behind employees. Corresponding needs are Company Policies, Supervision: Human Relations and Supervision: Technical.
- Independence — Occupations that satisfy this work value allow employees to work on their own and make decisions. Corresponding needs are Creativity, Responsibility, and Autonomy.
- Relationships — Occupations that satisfy this work value allow employees to provide service to others and work with co-workers in a friendly non-competitive environment. Corresponding needs are Co-workers, Moral Values, and Social Service.
Performance Measures
Internal Key Performance Indicators (Source: Internal data collections, and Post-Graduate Surveys)
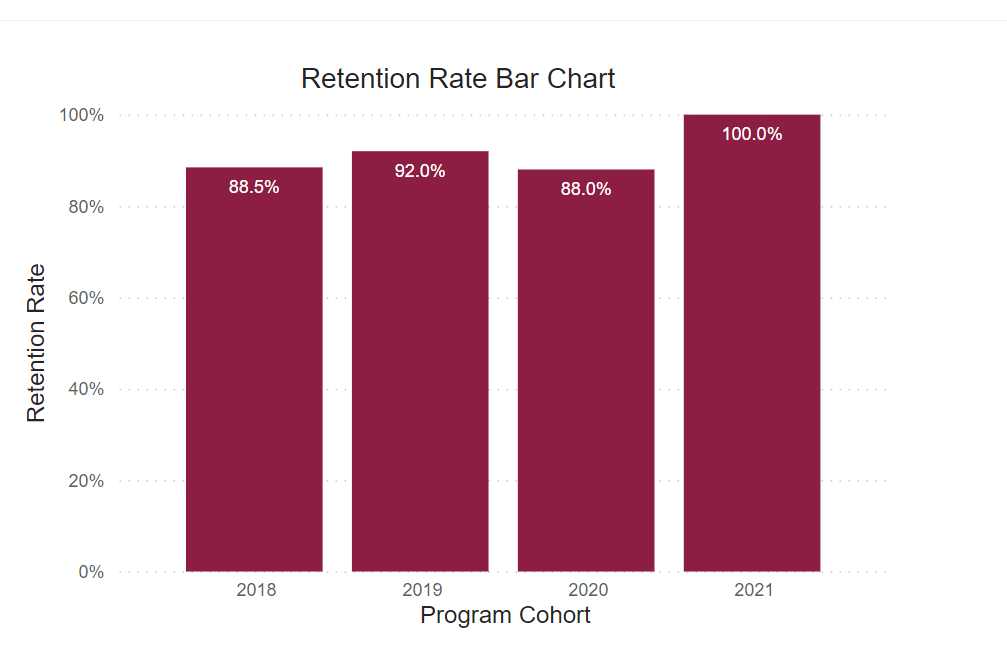
Retention Rate
This rate reflects the continuous term-to-term persistence rate for certificate programs and the fall-to-fall retention rate for associate degree programs.
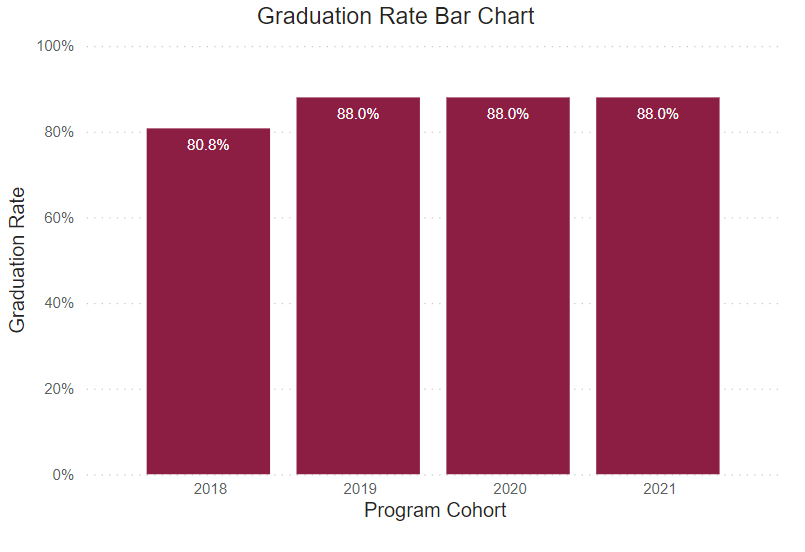
Graduation Rate
This rate reflects the number of freshmen who were officially enrolled in the fall semester and earned a certificate or degree within the expected timeframe.
Post Graduate Survey Response Rate
The post graduate survey is an annual on-line post graduate survey utilized by the college to gather vital information regarding career placement, starting salary, and level of satisfaction.
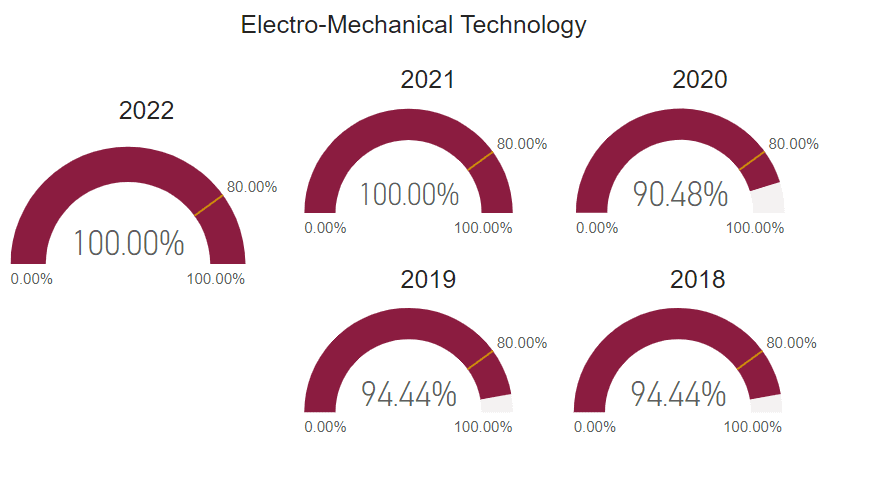
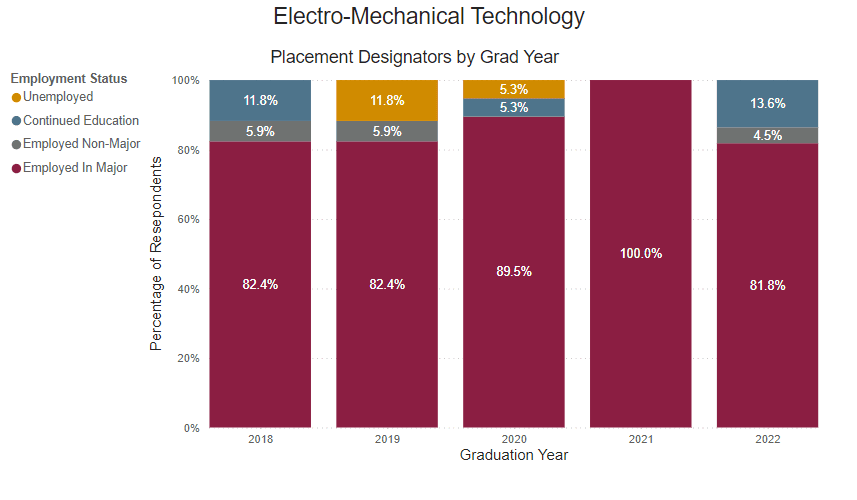
Employed Full Time Outside of Major
Percentage of graduates who reported being employed full-time outside their field of study.
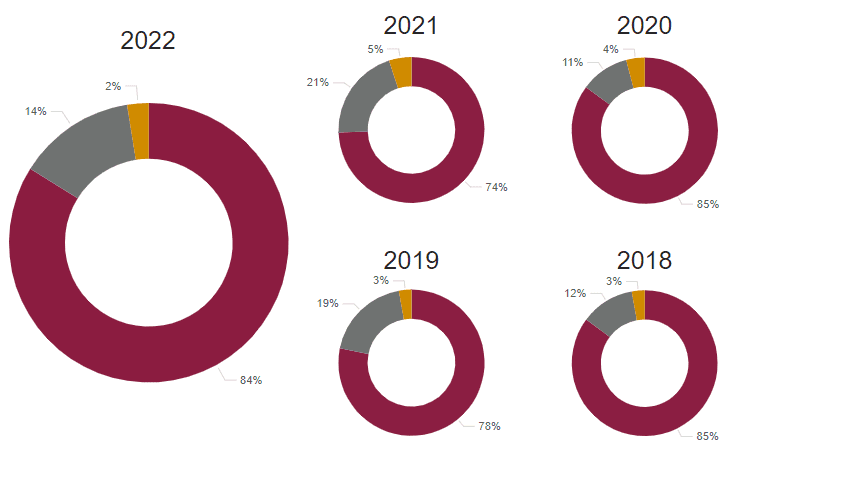
Graduate Satisfaction
This is the median graduate survey response evaluating the level of preparation for workforce entry (based on a 5-Item Likert Scale).
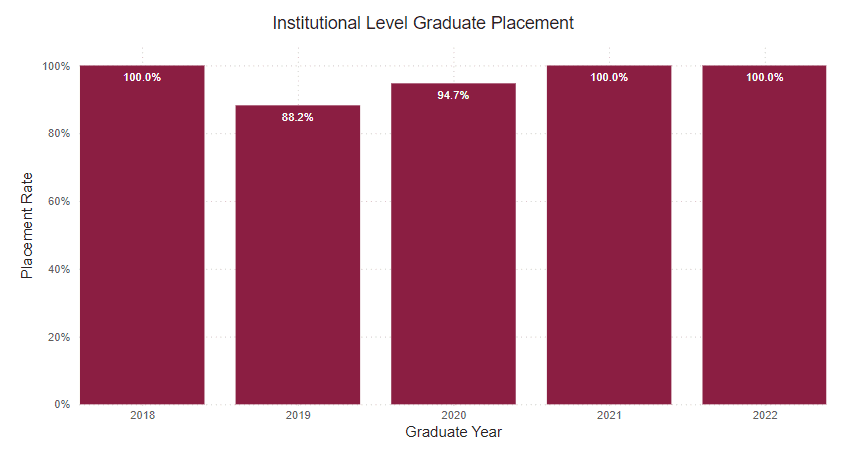
Placement Rate
This is the percent of graduate survey respondents who reported being employed or continued their education on a full-time basis.
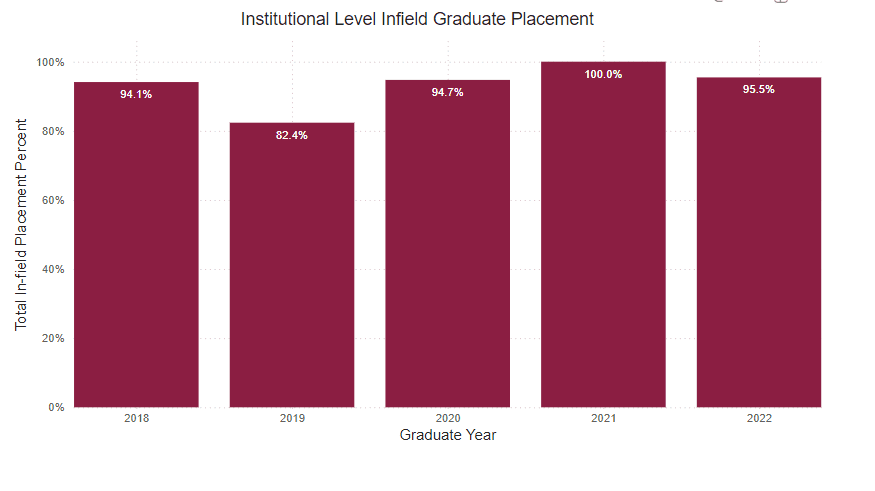
Employed Full Time Within Major
Percentage of graduates who reported being employed full-time within their field of study.
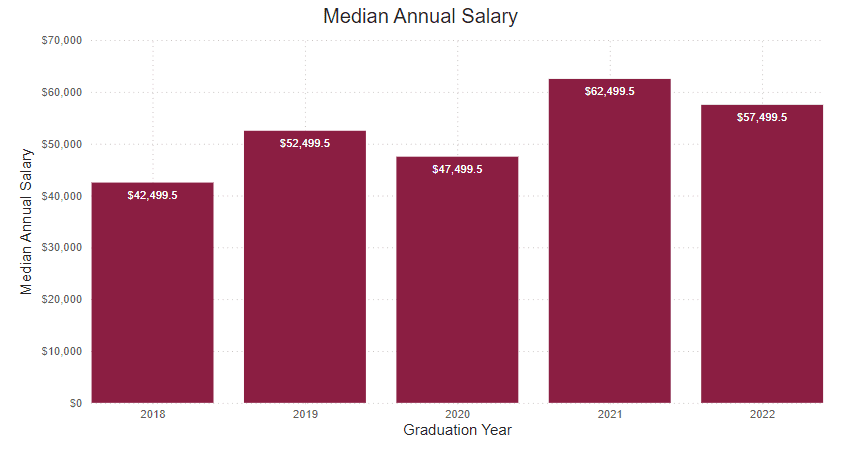
Annual Median Starting Salary
This number is based on the graduate survey response to the request to identify a starting salary from a range of options. This graph shows the median first-year annual salary. All calculations are based on the respondent’s self-reported first-year annual income.
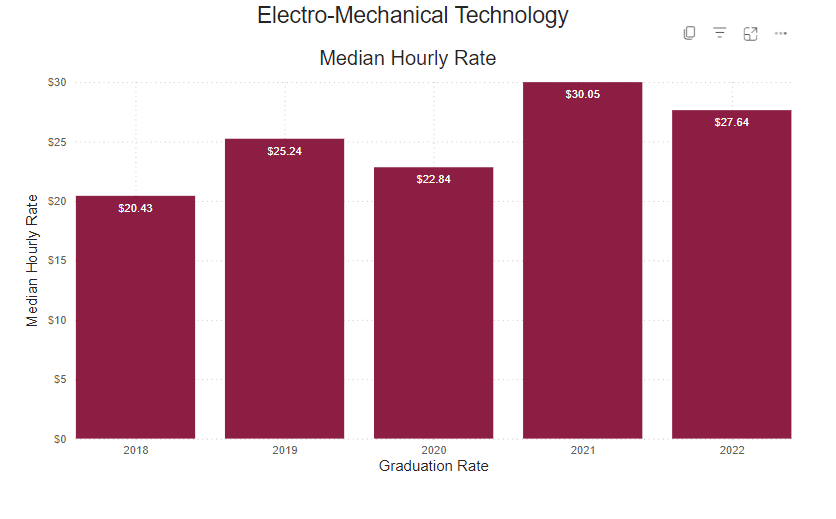
Reported Hourly Rate
This number is determined by dividing the reported median salary by the number of hours in a traditional full-time work week (40), then the number of weeks in a year (52).

Our graduates work with the industry’s best